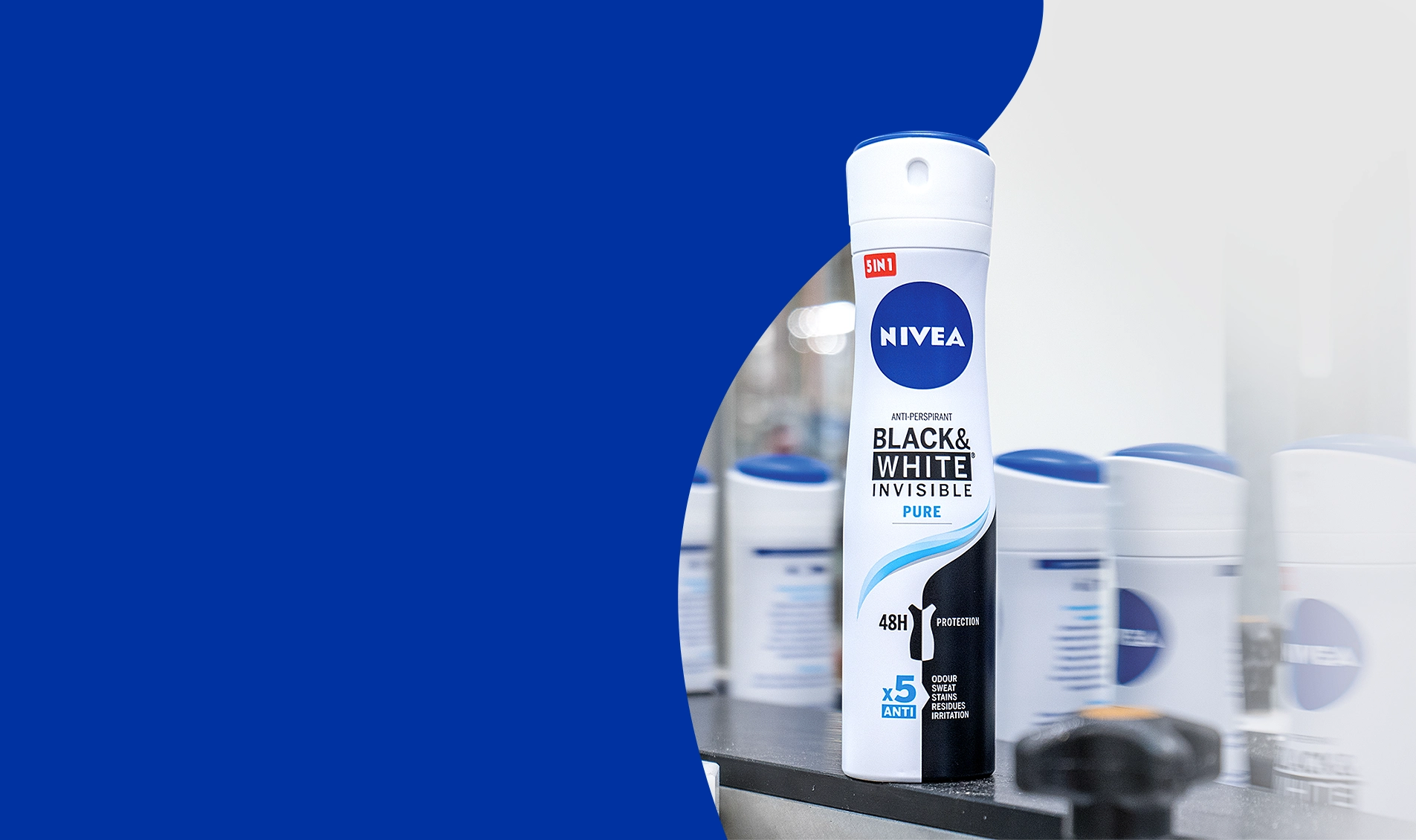
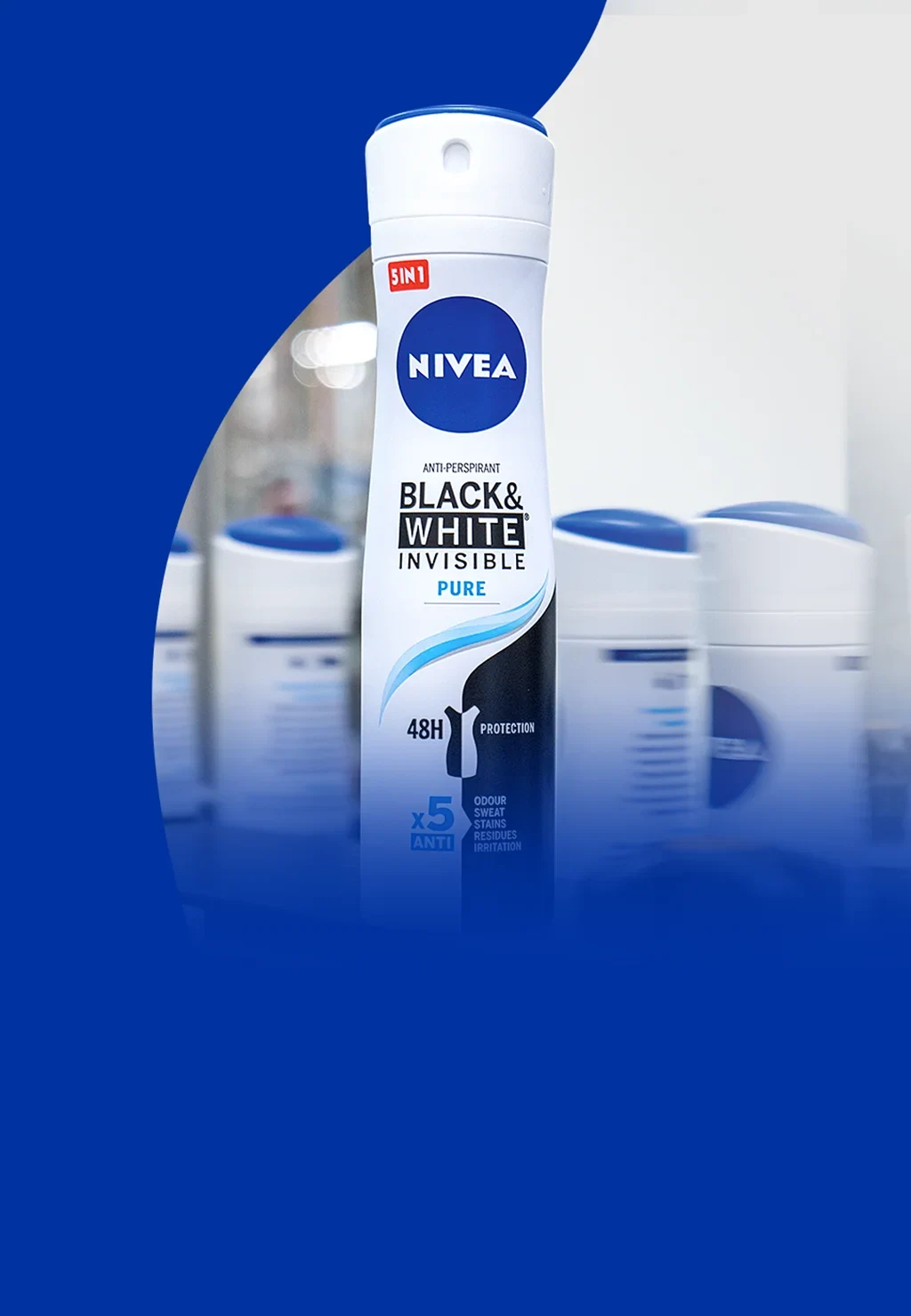
Supply Chain
Expansion for
Expansion for
further growth
further growth
Future-oriented production
Indonesia, Mexico, Poland, Vietnam: Beiersdorf is investing in the expansion of its plants around the world in order to significantly increase production capacity. This is because products from the brands NIVEA, Eucerin, Hansaplast, La Prairie, tesa, and many more are inspiring more and more people and enjoying strong growth in demand – in all regions of the world.
The Group even opened a completely new production center in Germany in 2023: At almost €300 million, the plant in Leipzig-Seehausen is the largest site investment in Beiersdorf’s history. In the immediate vicinity, a hub for Beiersdorf’s European supply chain network will also be built by 2027 with an investment volume of over €200 million.
The high level of investment in production and the supply chain is not only intended to meet growing demand. It will also set new standards in efficiency, resilience, and sustainability through the use of digital technologies and modular production principles.
> €1.3 bn.
invested by Beiersdorf in its production network since 2018
1.4 bn.
units can be produced additionally
> 6,500
employees work in Beiersdorf’s global supply chain
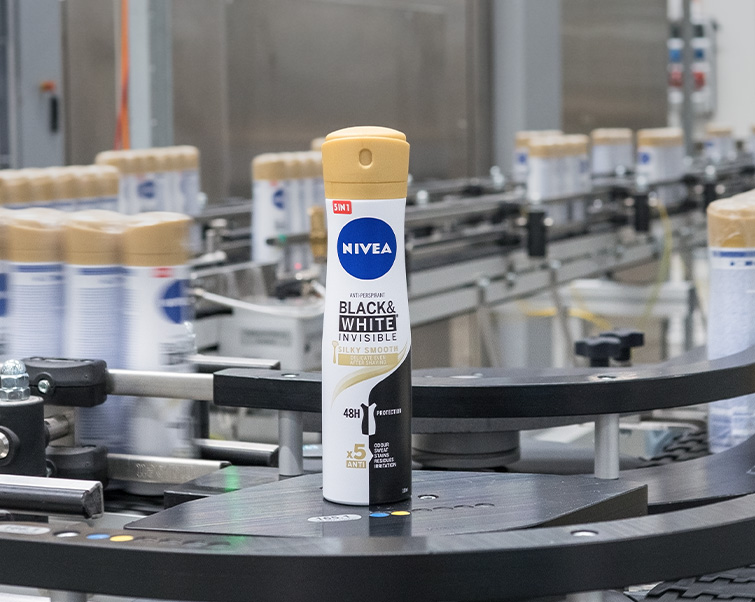
Up to 450 million cosmetic products can be made in Leipzig annually – in particular deodorants, hair sprays, and shaving creams for the entire European market and export.
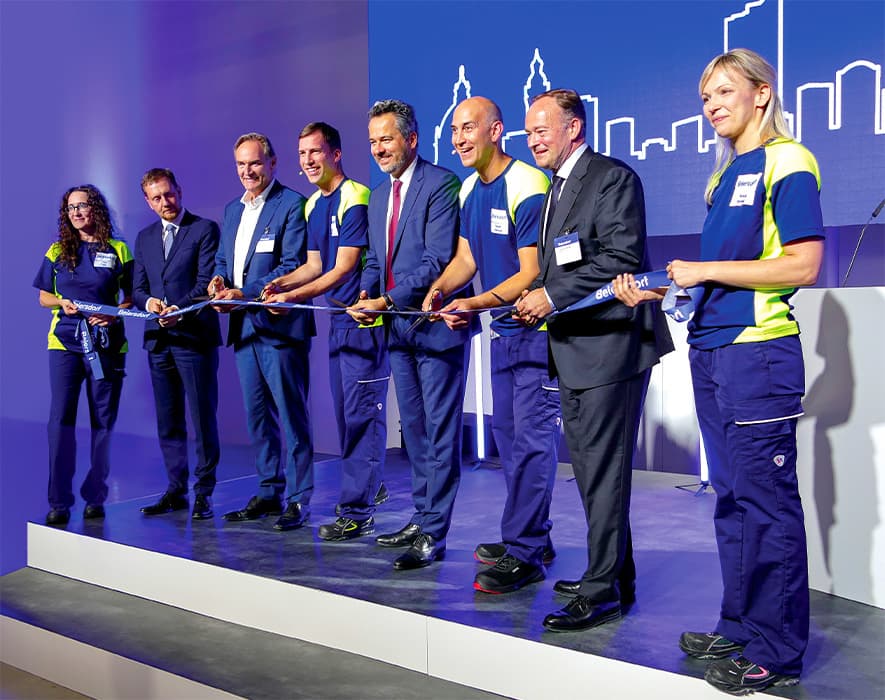
Opening ceremony of the new plant in Leipzig on September 22, 2023
Leipzig Innovation and efficiency
In 2023, Beiersdorf opened a new state-of-the-art production center in Leipzig-Seehausen following 2.5 years of construction. In the future, around 450 million cosmetic products will be manufactured annually on an area covering 32,000 square meters – for the entire European market and for export.
In order to be able to quickly pick up on and implement new innovations, trends, and production processes, production has a modular and flexible structure. A high degree of automation and comprehensive digitalization of all production steps ensure maximum efficiency and productivity.
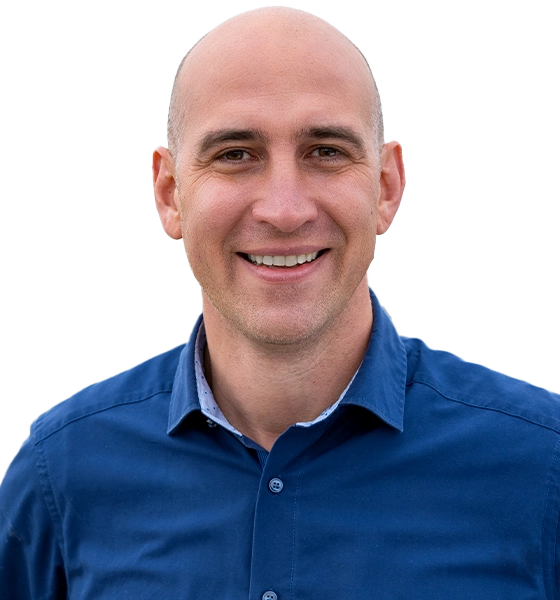
Dr. Tobias Rhensius
Project Director
The highest sustainability standards
The sustainable design of the plant in Leipzig will help Beiersdorf achieve the ambitious goals set in the company’s sustainability agenda CARE BEYOND SKIN. The facility meets the very highest environmental standards. The plant’s new technical capabilities will enable the company to introduce innovative and more sustainable packaging solutions to the marketplace - including aerosol cans made of recycled aluminum.
By using renewable energies and biogas to generate heat, the plant is nearly 100 percent carbon neutral. Valuable resources such as heat, waste-water, and ethanol will be recovered and recycled at the new plant.
The company plans to operate the plant as an Energy+ site and produce more electricity than it uses, thanks in part to photovoltaics.
Poznań From Poland to the whole world
Doubling production capacity, tripling storage space – all while production continues: Natalia Koryzna remains calm despite this mammoth task. “We have a very experienced, highly qualified team here that always finds practicable solutions and ensures full production efficiency,” says the head of Beiersdorf’s plant in Poznań, Poland.
The site has been systematically expanded since 2020 and around 150 additional employees have been hired since then. The work should be completed in the coming year. The plant in Poznań will then be one of the largest production units in the entire Group.
“Face care is the heart of our portfolio. It must be continuously improved in order to keep up with the latest trends and set new competitive standards,” Natalia Koryzna says. “This is why we have specialized in the introduction and scaling of new compounding technologies and packaging formats. Managing our complex production operation while expanding our location creates a special challenge for us – but it is also a wonderful task.”
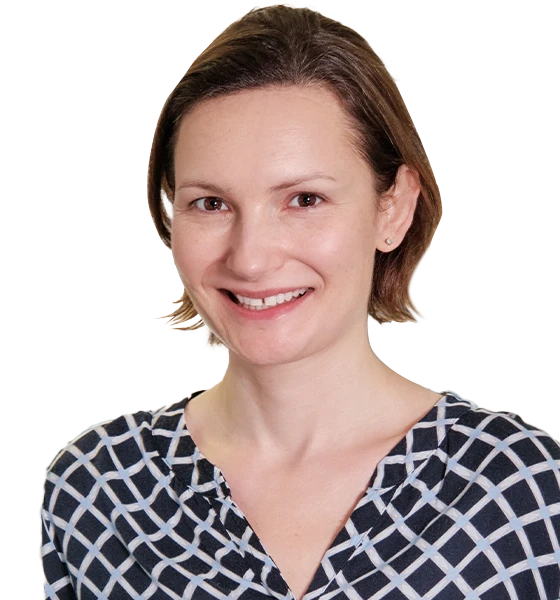
Natalia Koryzna
PC Director at Beiersdorf Manufacturing Poznań
Malang Products for an emerging market
Why was the plant in Malang, Indonesia, expanded?
Dwi Mudriah: “Demand for our deodorants and body care products in Indonesia has been growing by around 20 percent annually for years. That is why we increased the plant’s compounding and production capacity between 2020 and 2022 by 140 percent. In order to meet the rapidly growing interest in our products, the next expansion is already being planned.”
Why is it important to make products for Indonesia locally?
Dwi Mudriah: “Firstly, the Indonesian government has introduced restrictions on the import of goods, including cosmetics – primarily to protect local manufacturers. Secondly, it allows us to produce more specific products for target groups. This is important because all products for the Indonesian market will have to meet halal requirements by 2026. To achieve this, not only the products but also the production processes must be halal-certified.”
There is an above-average number of women in the supply chain team. Why is that?
Dwi Mudriah: “In fact, around 60 percent of my team is female. This is because the proportion of working women in Indonesia is very high. But it is also the result of our efforts to promote diversity. Because time and time again, we find that we are more successful when the perspectives and experiences of different people are brought together.”
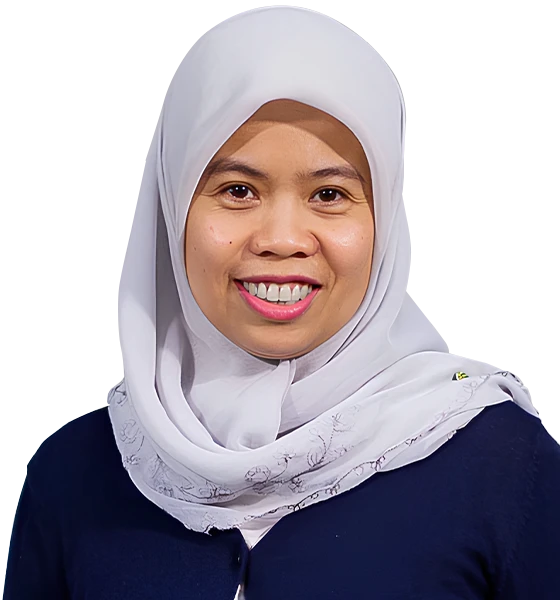
Dwi Mudriah
Supply Chain Director, Beiersdorf Indonesia
As a result, we have achieved gender parity across all management levels – thereby achieving Beiersdorf's gender parity ambition 18 months ahead of schedule.
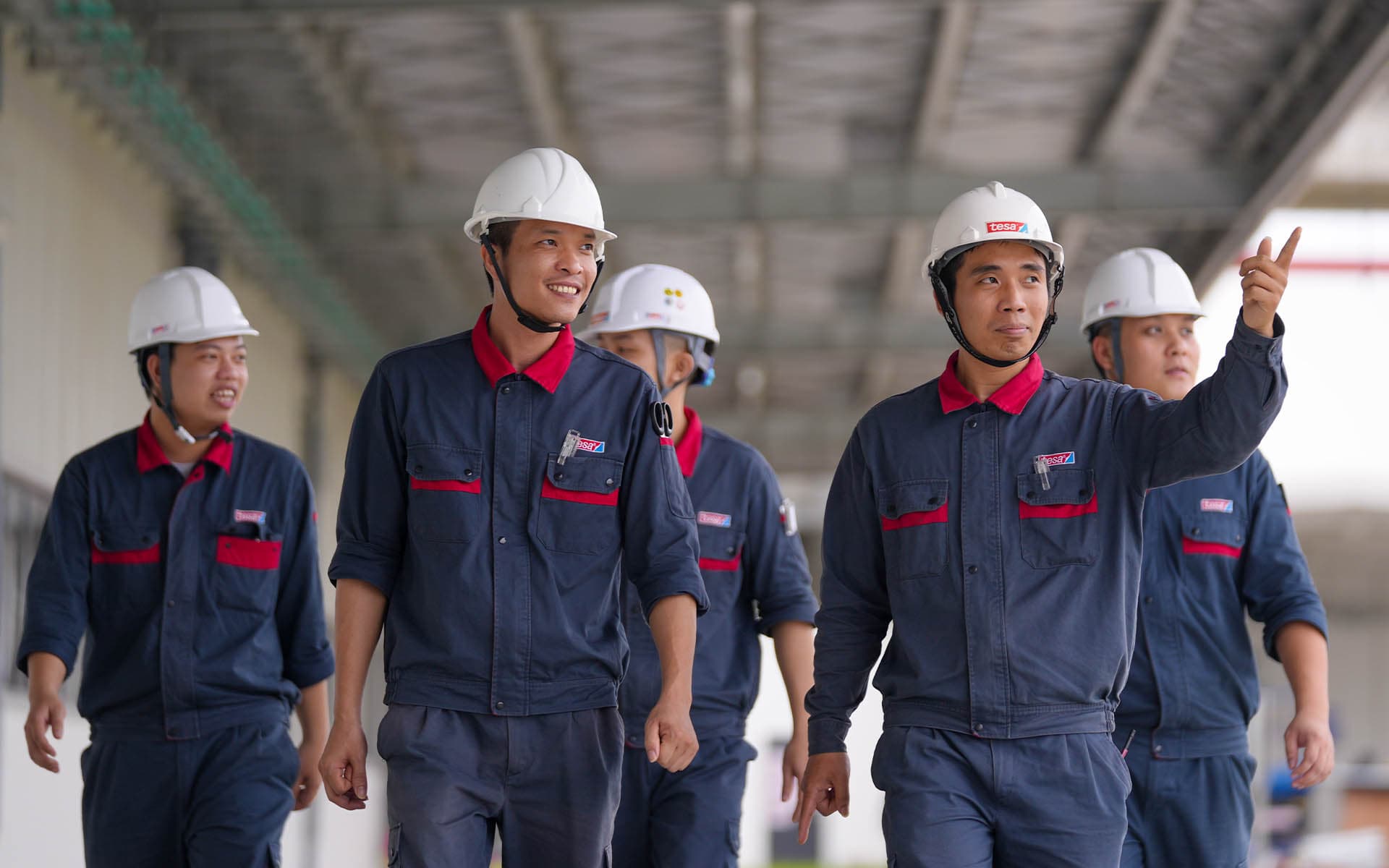
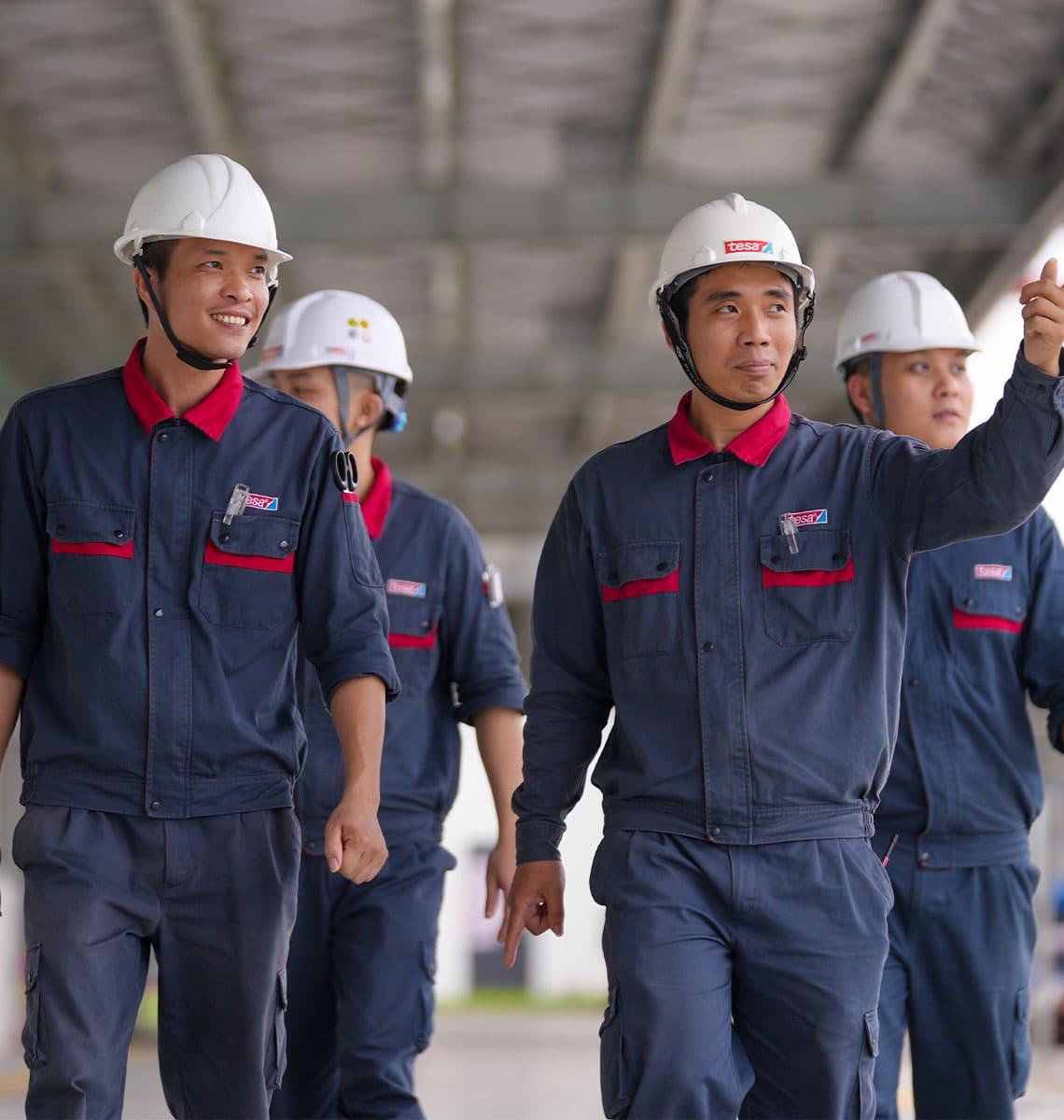
tesa at the pulse of the regions
tesa is driving forward its international expansion and strengthening its own supply chains: A state-of-the-art site was opened in the Vietnamese port city of Haiphong in October 2023 and the existing site in Sparta, Michigan, in the United States was converted to solvent-free production.
The new tesa site in Haiphong was built in just 18 months. It will produce 40 million square meters of adhesive tape annually, especially for the automotive and electronics industries. “We are proud of what the team has achieved within this ambitious schedule. The site, which was built in accordance with the LEED Gold Standard, has expanded our regional production capacities, meaning that we can supply our customers even faster and in a more targeted manner. In addition, 50 percent of the products manufactured in Haiphong are water-based adhesives,” says Stefan Schmidt, Head of tesa Supply Network.
tesa is also pursuing the goal of more sustainable production at its site in the United States, which has been expanded to a total area of over 16,000 square meters. “Thanks to the new solvent-free production facilities, the tesa site in Sparta has been able to significantly reduce its carbon footprint. This is an important milestone on the road to climate-neutral production by 2030. In addition, in the new Customer Solution Center, we can test products and application solutions extensively on-site with our North American customers and start production as quickly as possible,” adds Schmidt.
The global expansion of the production network is making supply chains more resilient and shorter. Together with international customers and partners, tesa continues to focus on developing innovative and sustainable adhesive solutions for the future.
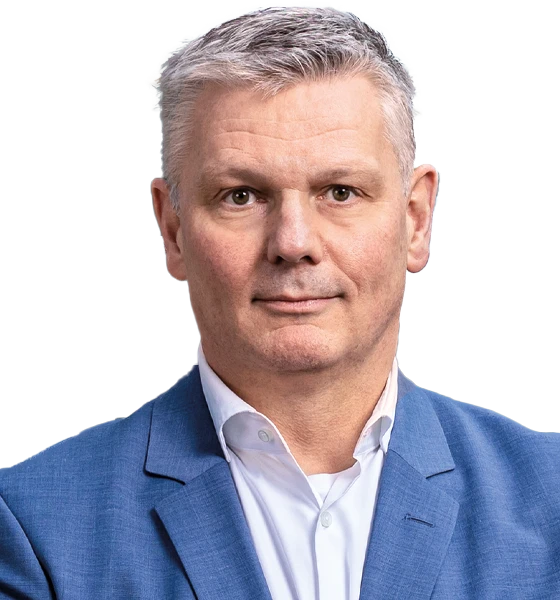
Stefan Schmidt
Head of tesa Supply Network